Machinery
Different needs,
best quality
High production cocoa presses
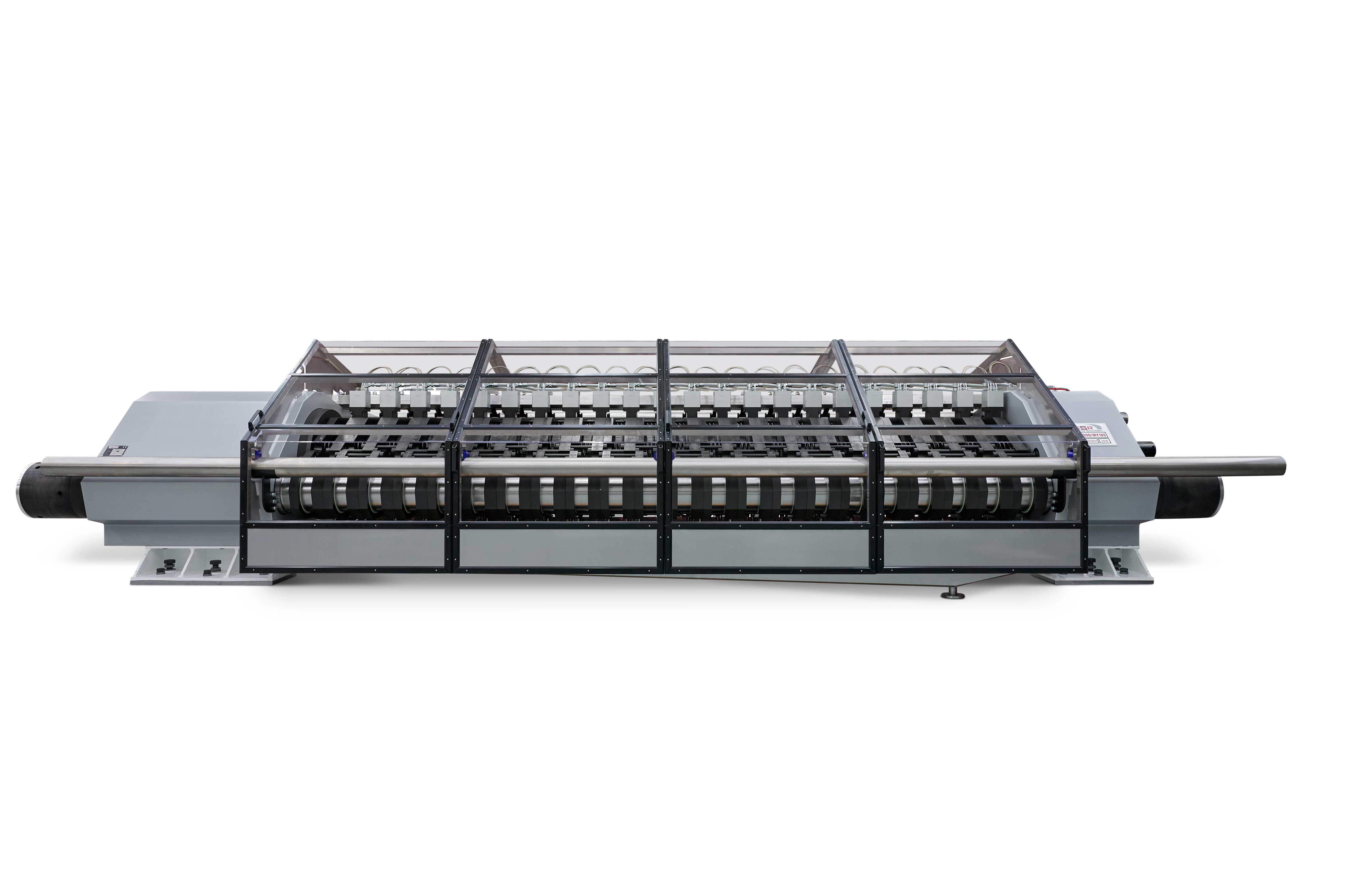
Series 990 | 980 | 900
With our series 900, 980 and the NEW 990 22V, we cover the full range as of productive capacity and we are able to manufacture a “tailor made” line, according to customers’ needs.All GSR’s presses meet the strict global standards required by the Company Management: quality in the first place and a refined Italian design, capable to ensure high ergonomics and hygiene; essential aspects for a perfect productive cycle.
Furthermore the special profiles, ensuring an excellent mechanical resistance in compliance with the requirements for energy saving and safety, feature the equipment with GSR’s standards of efficiency and reliability.
An accurate design of each press allows a remarkable reduction in machine downtime due to cleaning and maintenance.
The NEW 990 series deserves a special attention, a perfect mix between technological innovation and the highest production efficiency compared to the occupied space.
Productive capacities (low fat content cakes):
- series 990 up to 1950 kg/h
- series 980 up to 1540 kg/h
- series 900 up to 1060 kg/h
Series 990
With the series 990 we succeeded in further increasing the already excellent performances of the series 980.
In its design we set some fixed points referred to:
• production capacity compared to the occupied area
• efficiency
• energy consumption
• ergonomics
With our usual manufacturing philosophy combined to the high quality which set us apart, we reached our established goals with very encouraging results: a very high production capacity achieved with a small sized press.
It means we are able to supply high productive capacity compared to the occupied area.
Another essential aspect to be considered is a remarkable decrease of machinery down time due to cleaning and maintenance with a low tco (Total Cost Operation).
Technical Data
Productive capacity (low fat contents cakes):
up to 1950 kg/h
Series 980
With our Series 980 we cover the full range as of productive capacity.
As all other presses offered by GSR, also these big presses meet the strict global standards required by the Company Management: quality in the first place and a refined Italian design able to ensure high ergonomics and hygiene; essential aspects for a perfect productive cycle.
Furthermore the special profiles, ensuring an excellent mechanical resistance in compliance with the requirements for energy saving and safety, feature the equipment with GSR’s standards of efficiency and reliability.
A special treatment of all parts prevents any oxidation action, allowing the use of sanitizing products with no consequences.
Technical Data
Productive capacities (low fat content cakes):
up to 1540 kg/h
Series 900
Series 900 belongs to the category of the “big sisters” as of its own high productive capacity.
Among them, the press 8/900 deserves a particular emphasis. It has been studied to meet the current market trends aiming to achieve a 100% original product.
The press 8/900 belongs to GSR’s high productive capacity presses; nevertheless, as it is the smallest, it approaches also to the group of the compact lines.
This press is able to ensure the right qualitative mix between the two ranges, by placing exactly halfway between the productive philosophy of the “big sisters” series 900-980-990 and the compact one Series 870.
The press 8/900 represents for GSR the right completion of Series 900.
Comparatively small but with a huge inner potential, able to ensure productions suitable also to the necessities of middle-sized companies.
In general its features are:
- - low managing costs
- - easy and fast installation
- - high flexibility
Technical Data
Productive capacity (low fat content cakes) up to 1060 kg/h
Compact presses
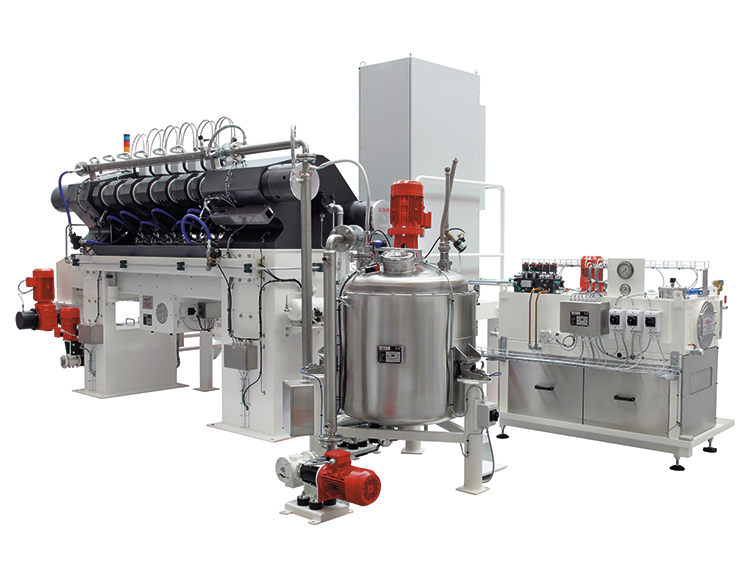
Series 870
Our compact series 870 has been specifically studied for all companies requiring lower capacities than the high production presses ones.These compact lines consider the use of our presses series 870 which manufacturing philosophy is the same of their “big sisters” of 900, 980 and the NEW 990 series.
Their unique features are:
- Easy and fast installation
- High power and flexibility
- Low managing costs, Total Cost Operation
- High automation standards
- Advanced pressing process control
- High process efficiency
Productive capacities (low fat content cakes)
Series 870 up to 450 kg/h
Presses production accessories
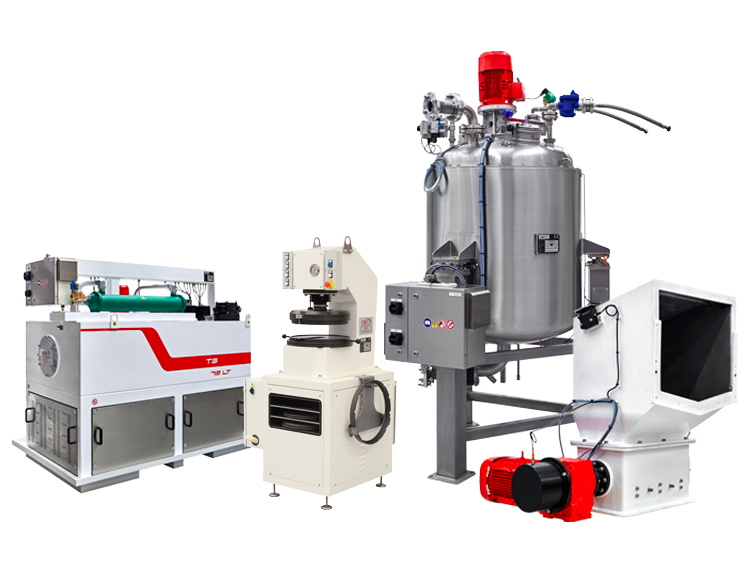
Presses Accessories
To complete our production presses, we propose some essential accessories for the presses operation:- Hydraulic group series T3
- Homogenizer series CT
- Product transfer pumps series P4
- Butter scale series BT
- Cakes conveyor series TS
- Cake breaker series G
- De-dusting filter
- Press for the filter holding plate mounting type PMT
Cakes conveyors series TS
Solid structured conveyor, properly designed to collect cocoa cakes falling down from presses and to feed the cake breaker.
It is equipped with a pusher, controlled by an inverter managing the advancing speed and intermediate breaks programmable by the software for the best grinding.
Specifically designed to reduce the noise level during the cakes release.
According to the press typology, models of various lengths are installed: from 3000 mm. up to 8100 mm.
Technical Data
Lenght: from 3000 to 8100 mm
Press for the filter holding plate mounting series PMT
The press for the filter holding plate mounting series PMT has been designed to ensure an easy, fast and correct assembly of the filer cloths on the filter-holding plates, essential condition to guarantee a longer life of the filter cloths.
This specific equipment ensures the centering of the filter cloths with respect to the plate, a proper positioning of the cloth as well as the insertion of the Teflon cord to be pressed in the seat, through an hydraulic group, for a perfect fastening of the cloths on the plate with an even tension.
The double push-button station with simultaneous activation system ensures a safe use, in compliance with the most restrictive safety rules.
Technical Data
Productive capacity: from 1360 kg/h to 2880 kg/h
Specific pressure on product: 980 kg/cmq
Hydraulic group series T3
Its mechanical/hydraulic design and the components choice, combined with an advanced managing software, allowed to realize these hydraulic groups, unique in their kind.
Our series T3 adapts to any pressing line, offering a remarkable production increase, quantifiable in a 30% more than the traditional hydraulic groups.
The strong points of our hydraulic groups are:
- - flexibility in adapting to the various kinds of liquors to be pressed;
- - steady pressing curves with immediate and easy setting;
- - efficient management system, which can be interfaced with any kind of installation;
- - low maintenance.
According to the press productive capacities, the following models are used:
- - T3/45 LT – capacity up to 45 l/min – installed power 24,2 kW
- - T3/66 LT – capacity up to 66 l/min – installed power 32,2 kW
- - T3/75 LT – capacity up to 75 l/min – installed power 32,2 kW
Technical Data
Capacity: from 14 to 75 l/min
Installed Power: da 9,7 a 32,2 kW
Homogenizer series CT
This homogenizer has been properly designed to get, in the shortest possible time, the best preparation and conditioning of the cocoa mass to be pressed.
Thanks to its unmatched system, it ensures a perfect product homogenization, reducing the time by 35%, an essential aspect for the new productive necessities.
Totally built in stainless steel, it is assembled on loading cells to get an accurate weighing value of the product loaded into the press.
According to the press typology, the following models are installed:
• CT/400 – capacity 400 kg
• CT/500 – capacity 500 kg
Technical Data
Capacity: from 100 Kg to 600 Kg
Cake Breaker Series G
The aim of the cake breaker is to break cocoa cakes into uniform pieces to be conveyed to storage silos.
It is complete with hopper to be directly assembled on the cake conveyor.
Equipped with a clutch for emergency stop just in case, by accident, a metallic part falls inside.
Based on customer’s size requirements, the inner grid may be adjusted.
According to the press typology, the following models are installed:
- G65S
- G75S
Technical Data
Model G35S: capacity beyond 1500 kg/h
Model G65S: capacity beyond 3000 kg/h
Model G90S: capacity beyond 3500 kg/h
Scales Series BT
Its duty is to weigh the butter got from pressing.
Totally made in stainless steel, it is assembled on a loading cell for a steady monitoring of the quantity of product inside.
An heating system keeps butter in a liquid state even if the automatic pressing cycle stops for a long time, avoiding so the failure of the unloading pump.
According to the press typology, the following models are installed:
- BT/150LT capacity 150 litres
- BT/200LT capacity 200 litres
De-dusting filter
The de-dusting filter is certified and suitable for filtering potentially explosive dust. It is equipped with a burst panel and in compliance with ATEX-D Rules for application with dust classified St.1
Made of galvanized sheet metal, it is suitable for outdoor installation.
Its suction and filtration system sucks up cocoa dusts delivering them, through the suction piping,
to the filter; here the fabric sleeves hold the dust dispersed in the air.
The filtered dust is collected in a dumpster.
According to customers’ necessities, there are three models with different capacities
- 1500 m3/h
- 4500 m3/h
- 9000 m3/h
Technical Data
Filtering air flow: from 1500 m3/h to 4500 m3/h
De-dusting filter
The de-dusting filter is certified and suitable for filtering potentially explosive dust. It is equipped with a burst panel and in compliance with ATEX-D Rules for application with dust classified St.1
Made of galvanized sheet metal, it is suitable for outdoor installation.
Its suction and filtration system sucks up cocoa dusts delivering them, through the suction piping,
to the filter; here the fabric sleeves hold the dust dispersed in the air.
The filtered dust is collected in a dumpster.
According to customers’ necessities, there are three models with different capacities
- 1500 m3/h
- 4500 m3/h
- 9000 m3/h
Technical Data
Filtering air flow: from 1500 m3/h to 4500 m3/h
Product transfer pumps series P4
These pumps have been properly designed to transfer products among the different utilities.
Manufactured with special steels, all parts in contact with the product are treated and hardened to ensure a long life of the seals.
They need a very low maintenance.
The model used for press loading has got high delivery in order to reduce the loading time.
P4/400HMMC (press loading):
• delivery 450 kg/min
• power 11 kW
• max. pressure 16 bar
P4/190VHMMC (butter unloading):
• delivery 155 kg/min
• power 3 kW
• max. pressure 2 bar
Technical Data
Filtering air flow: from 1500 m3/h to 4500 m3/h
Coolers
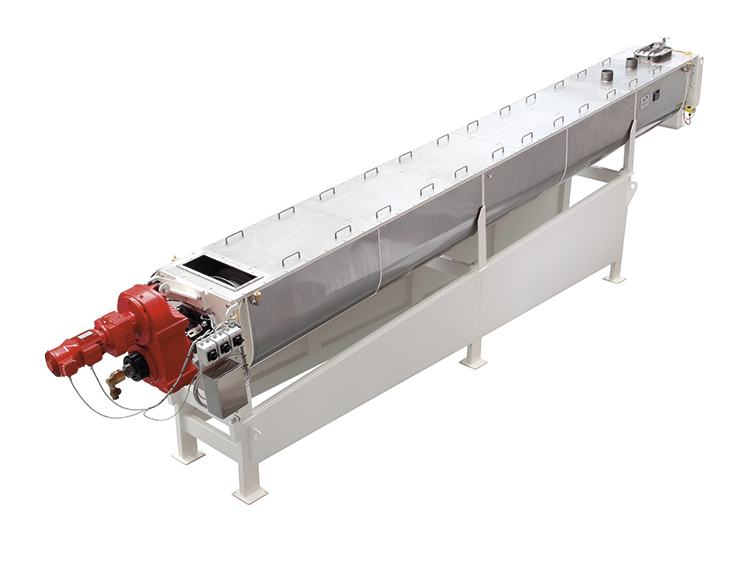
Coolers series CSS | Dessicated Air Unit
To avoid any problem by conveying high temperature crushed cakes, there is the possibility to add the pressing line our cooler series CSS, to lower product temperature.To facilitate this process there is the possibility to equip the cooler with a desiccated air unit blowing dry air into the cooler in order to avoid moisture formation.
Coolers series CSS
Their duty is to cool/condition the crushed cakes, coming from the cake breaker, as first stabilization.
They are indirect heat exchangers, lowering the temperature of the crushed cakes from 90°C to a temperature of 40/45° C. Then the crushed cakes will be conveyed to the next operative phases avoiding so any contamination which might occur by conveying high temperature crushed cakes.
Our solutions to use multiple cooling chambers to mitigate the impact , matched to a dry air feeding system, allow to accurately adjust the wished cooling process and avoid moisture formation.
Technical Data
Cooling capacity: up to 1000 kg/h
Specific pressure on product: 990 kg/cmq
Dessicated Air Unit
The target for the desiccated Air Unit is to maintain the best hygrometric conditions inside the cooler series CSS, eliminating so the moisture formation inside.
Upon request the desiccated air unit can be equipped with pre-and-post cooling battery.
Technical Data
Productive capacity: from 1360 kg/h to 2880 kg/h
Specific pressure on product: 980 kg/cmq
Filtering
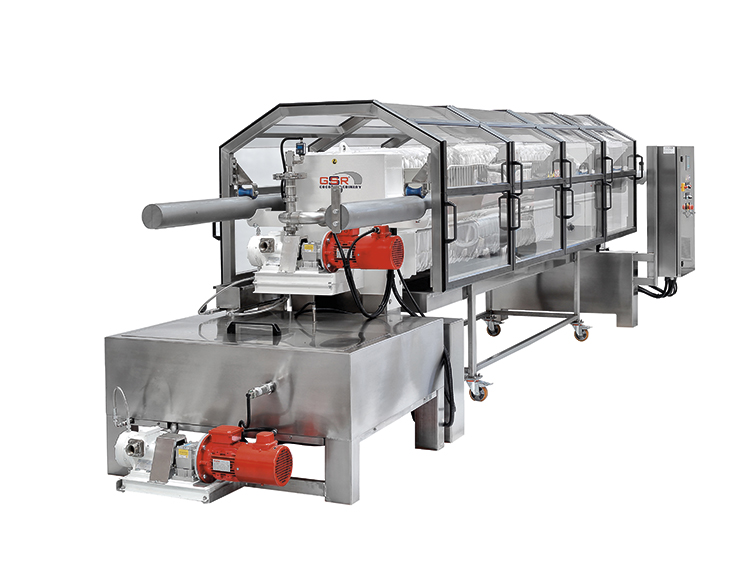
Filter Press | Cricket Filter
To improve the quality of the butter got from pressing, eliminating as much as possible the impurities inside, it can be used a filtering system.According to the productive capacity there are two systems:
The filter press
The filter cricket
Cricket Filter
The filter equipment for cocoa butter with filter cricket consists of a filter, provided with filtering elements and heated by hot water, and other auxiliary machines performing the following functions:
- Feeding and filtering pumps which feed the filter cricket with the butter to be filtrated
- Two hoses filters for a second filtration phase
- Various kinds of pumps which transfer the filtered product and the sludge into proper tanks
- A compressed air equipment providing the cleaning of the filter elements.
In general the specific functions of the equipment are the following:
- To filter the cocoa butter
- To convey the filtered butter to the storage tank
- To convey the sludge to the proper storage tank
Technical Data
Filtering capacity: from 2000 kg/h
Filter Press
The filtering is made though a fabric having well defined flows and permeability characteristics.
The product to be filtered, pushed by the feeding pump into the filtering elements, has to flow, in its liquid state, through the fabric, giving so the solid particles which will be held by the cloths.
This happens until the cavities (of the filtering element) able to hold solids, are completely overfilled.
The check of this condition is made through a pressure switch which stops the filtering process once the press overcomes the max. pressure threshold.
The machine is composed of a steel frame in stainless steel where it is lodged the structure supporting the filtering couples (plates-frame-filters) and of a closing piston of the filtering pack.
On the frame there are the control panel, the feeding pump, the filtered butter collecting channel as well as the opening/closing plates device.
Technical Data
Filtering capacity: from 400 kg/h to 1500 kg/h